Die Technology – applications
The automotive industry: origin of single pair Ethernet.
Die Technology – applications
THE AUTOMOTIVE INDUSTRY: ORIGIN OF SINGLE PAIR ETHERNET.
The development of single pair Ethernet (SPE) began in the automotive industry, where smaller and more powerful devices were required.
More and more Ethernet systems are being installed in today’s vehicle generations. New driver assistance systems – such as lidar (light detection and ranging), high-resolution displays, 4K cameras or infotainment systems – can only be realized by networking control units and sensors. Future-oriented technologies such as autonomous driving also require a connection technology that enables transmission of higher data rates in a small installation space. Other industries can also benefit from this approach.
First official IEEE standards
The development of automotive Ethernet has resulted in two official IEEE standards: 100BASE-T1 (100 Mbit/s) and 1000BASE-T1 (1 Gbit/s). When defining these standards, the aim was to define the limits for connectors and cables as well as the measurement methods from the requirements for the overall channel (defined in the IEEE).
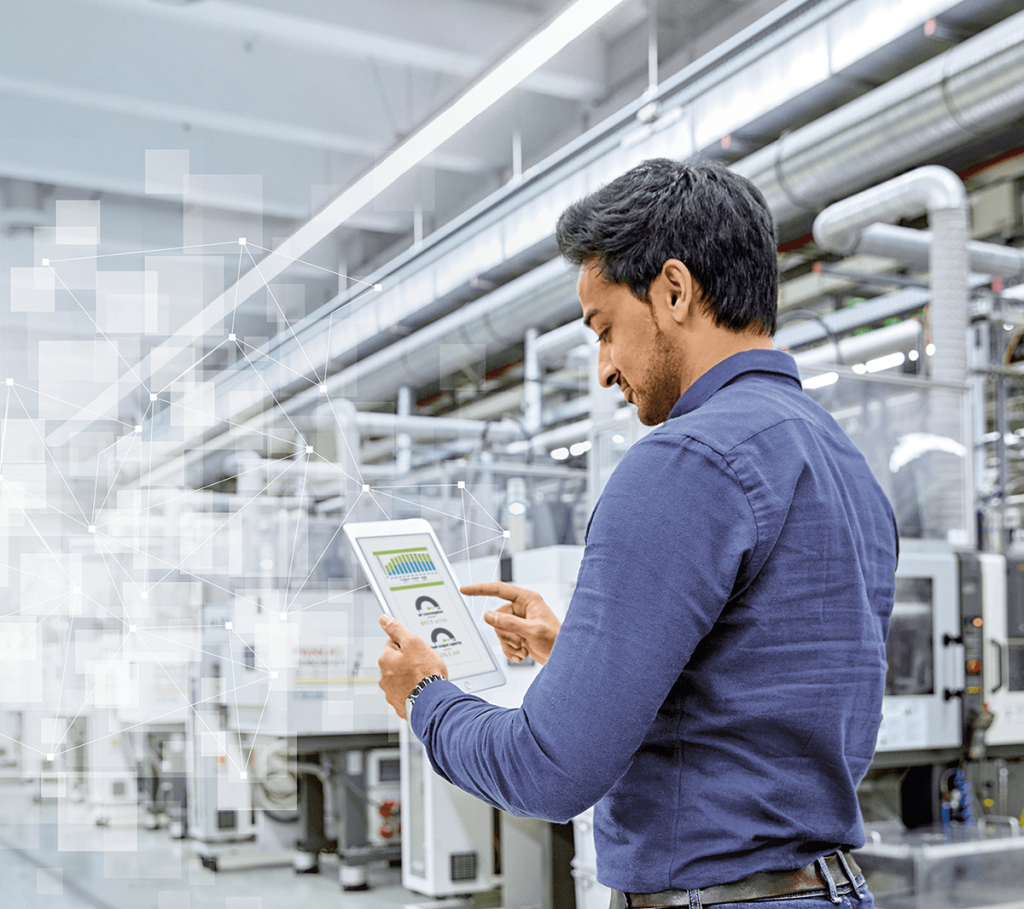
Application areas of SPE solutions
Single Pair Ethernet is ideal for infrastructure applications in mechanical and plant engineering, process technology, building infrastructure and many more.
The big advantage:
Single Pair Ethernet is environment neutral, so field devices, sensors and actuators can be easily integrated into an existing Ethernet environment. Additional gateways and interfaces are not required. Unlike fieldbus protocols, Ethernet penetrates all automation levels.
It is more consistent, efficient and cost-effective than fieldbus systems.
Advantages:
- Transmission distances of up to 1,000 m at transmission rates of 10 Mbit/s
- Transmission distances of 40 m at transmission rates of 1Gbit/s.
- Simple installation via only one pair of wires
- Reduction of space and weight
- Lower acquisition costs for new installations
- More compact cable trays
- Efficient cabling of multiple communication participants thanks to shared lines and interfaces (multidrop)
- Existing cabling can continue to be used
- Integration of up to four devices
- Tighter bending radii possible for cabling
Thanks to the standardized interfaces, single-pair and four-pair cabling concepts can be combined, as can IP20 and IP6x solutions. The two-wire technology also allows the application-specific supply of terminal devices with power of up to 60 watts via the same wire pair (Power over Data Line – PoDL).
— MUST BE INSERTED VIA HTML! —
Wiring requirements
Different applications have different cabling requirements. The relevant
Refer to the following table for cabling requirements:
Automotive industry | Building automation | Process automation | Factory Automation | |
---|---|---|---|---|
Application focus | Car wiring harness | Control cabinet wiring Field wiring (e.g. KNX) | Field wiring sensors | Ind. Control cabinet wiring Field wiring Sensors |
Transmission rate Transmission link |
10 MBit/s – 1 GBit/s 15-40 m |
10 MBit/s – 1 GBit/s < 1000 m | 10 MBit/s < 1000 m | 10 MBit/s – 1 GBit/s ≤ 100 m |
Conductor cross section | AWG 26-22 | AWG 26-22 | AWG 22-18 | AWG 26-22 |
Mech. / electr. Robustness | medium - high | low - medium | high | medium - high |
Current connections | Automotive specific connectors | Individual wiring, terminal, EIB, RJ45 | Terminal, connector, M12 | RJ45, single wiring, terminal, M8/12 |
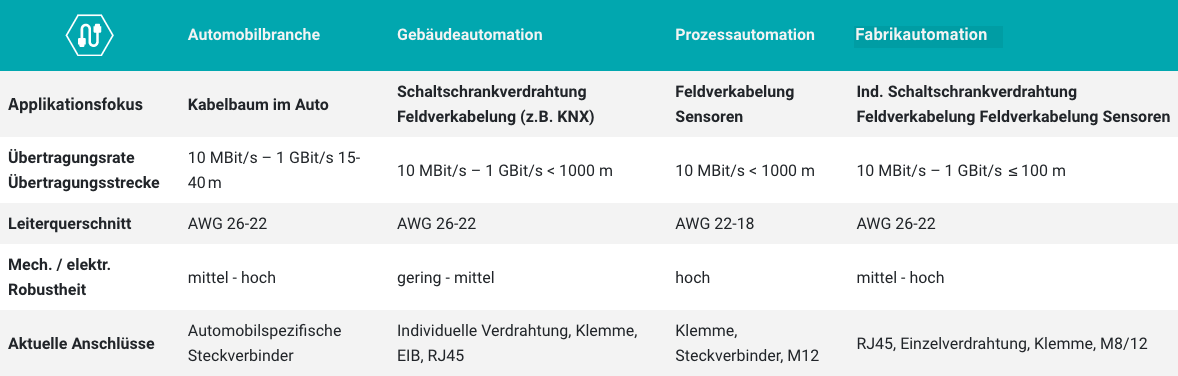
Connection technology in factory automation
With advancing automation, a growing number of sensors and actuators are being used in all areas of manufacturing, which must be reliably connected to cloud systems.
Single pair Ethernet solutions offer significant advantages here:
- Future-proof: Standardized connectors and cables according to IEC 63171-2 (IP20) and IEC 63171-5 (IP67)
- Powerful: ranges up to 1,000 m, data rates up to 1 GBit/s and power up to 60 W
- Efficient: Plug-and-play integration possible even with existing cabling infrastructures
- Compact: Plug-in faces for single and multiports allow high packing densities
- Integration-friendly: plug and socket variants for M8 inductive sensors and flying leads
The standardized IEC 63171-2 (IP20) and 63171-5 (IP67) interfaces are ideal for office and industrial environments. The application-optimized cabling forms the basis for future-proof networking from the sensor to the cloud.
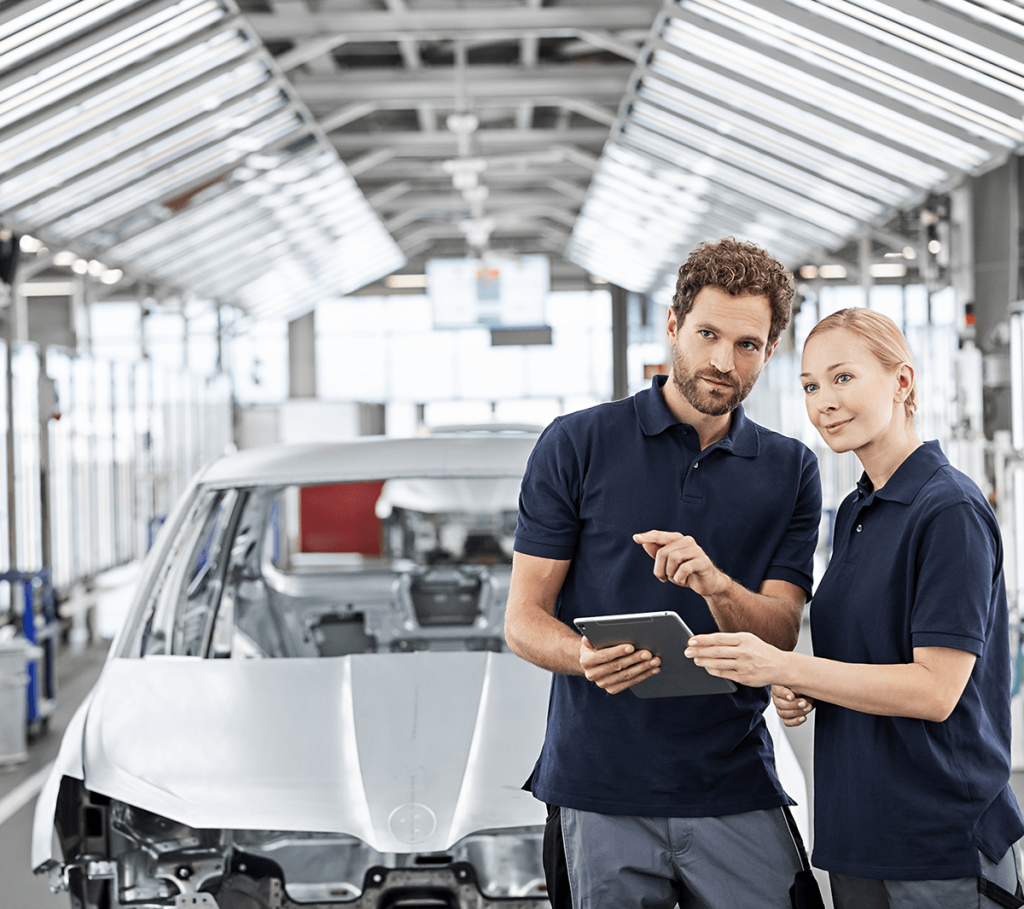
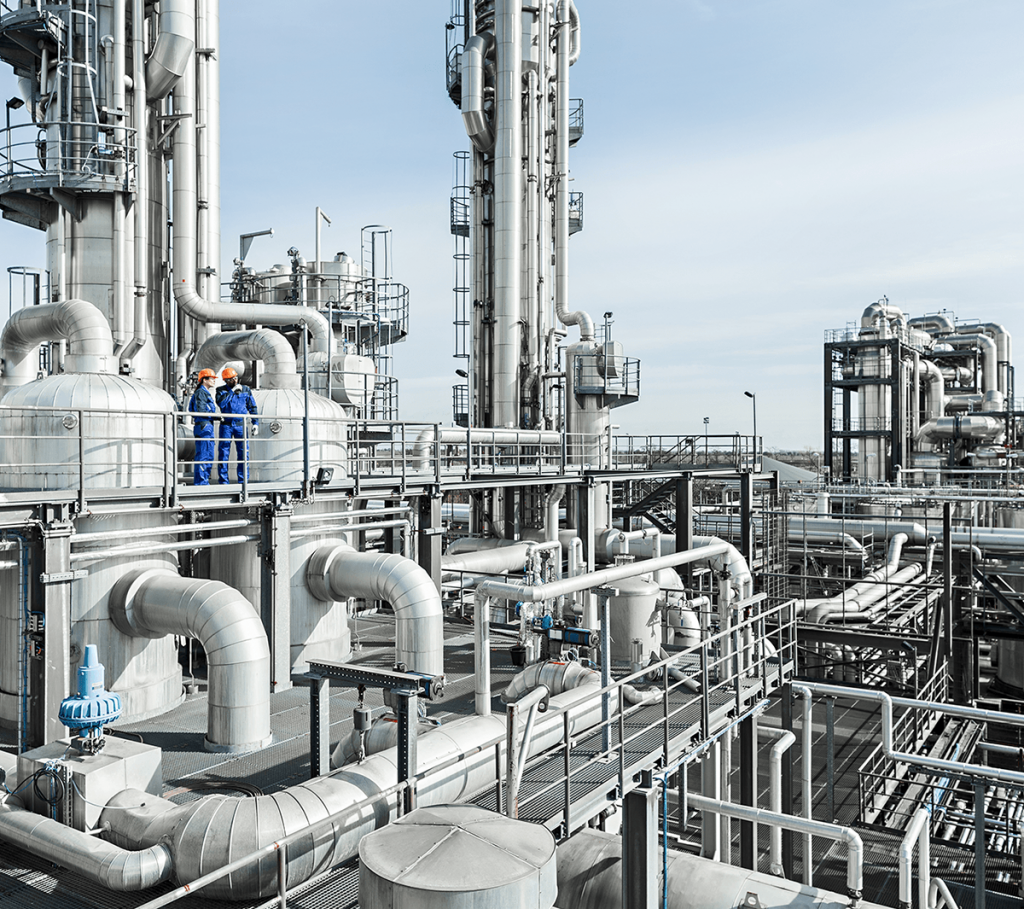
Connection technology for process automation
In process automation, explosion protection and long transmission distances place increased demands on network technology. The necessary standards are summarized as Advanced Physical Layer (APL).
Single Pair Ethernet solutions offer the following additional advantages for process automation:
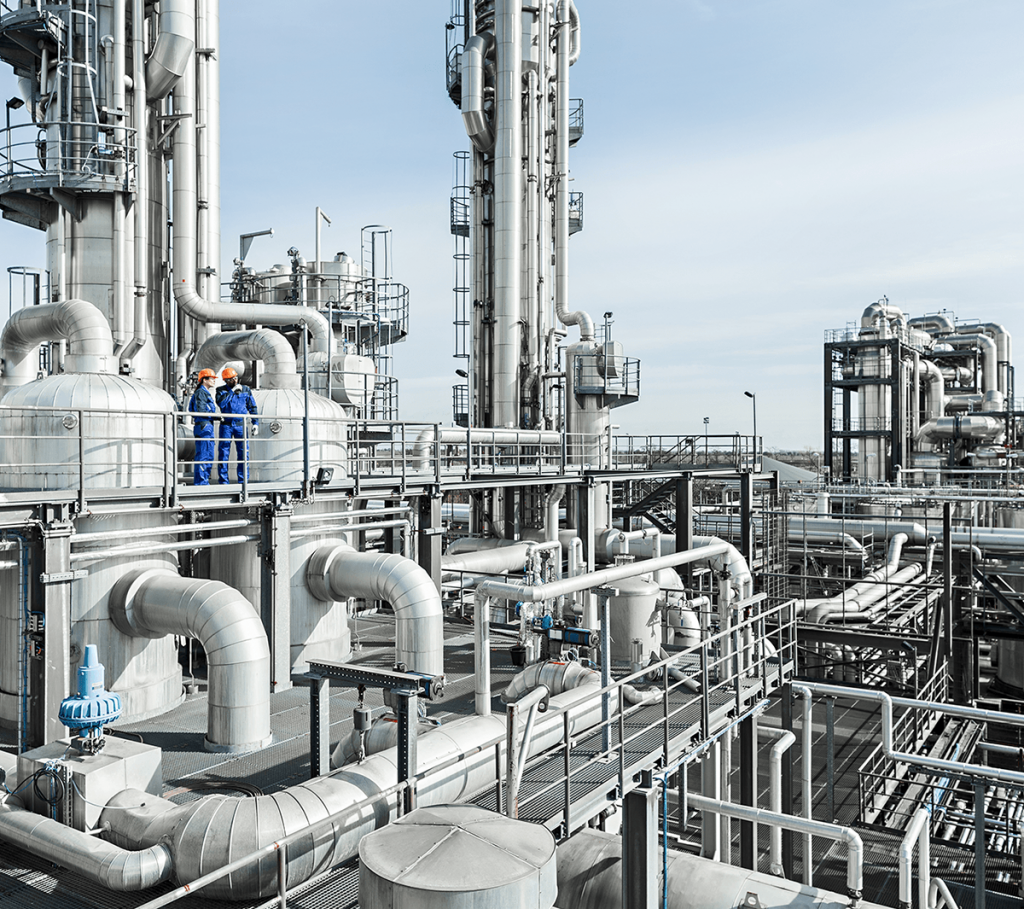
- Standard-compliant: All products meet requirements of the "APL Port Profile Specification" (Draft 0.3)
- Flexible: Horizontal, vertical and angled conductor connection direction for any device design
- Convenient: colored coding and labeling for easy wiring
- Safe: Also available for increased safety requirements in EX areas according to IEC 60079-7
Connection technology for building automation
The Internet of Things (IoT) has become an integral part of building automation and will continue to play an increasingly important role in the future. By using the IP protocol, building automation can be implemented both more conveniently and more cost-efficiently, as sensors, controllers and other technical units in the building are networked directly with the building management system. Thus, existing proprietary fieldbus systems are replaced by consistent Ethernet cabling, eliminating expensive and time-consuming programming and parameterization efforts.
The trend in the development of smart buildings is to reduce the energy consumption of all networked devices. This is another area where Single Pair Ethernet comes into its own, as high-performance transmission of data and power in parallel via just one twin wire is possible using Power over Data Line. Likewise, the single pair Ethernet components are robust and powerful and are versatile due to the different transmission distances and rates in combination with the high packing density.
